What is Design for Manufacturing (DFM)?
- alexandermangelo
- Jan 5
- 4 min read
In the competitive landscape of modern industry, where efficiency and innovation are critical, Design for Manufacturing (DFM) has emerged as a key methodology. This approach integrates manufacturing considerations into the design phase of a product, ensuring that production processes are streamlined, cost-effective, and free from unnecessary complexities. By fostering a close relationship between design and manufacturing, DFM enables faster time-to-market, reduced production costs, and high-quality output.
DFM serves as a practical framework for aligning creative product designs with the realities of manufacturing capabilities. It is widely regarded as a best practice in engineering and product development, helping organizations achieve a balance between performance, quality, and cost.

Why DFM Matters
The design phase of product development is crucial, as it determines a significant portion of a product's lifecycle cost—up to 80%, according to some studies. Addressing manufacturing considerations at this stage helps prevent costly redesigns, material wastage, and production inefficiencies.
In today’s fast-paced markets, where speed and cost-effectiveness are paramount, DFM has become indispensable. By tackling manufacturability challenges early, companies can avoid production delays, disruptions, and quality issues later in the product lifecycle.
Principles Guiding DFM
Standardization of Parts and Processes
Standardizing parts and processes involves using common components and procedures across multiple products or product lines. This strategy simplifies procurement, reduces inventory requirements, and minimizes the complexity of assembly operations. For instance, using off-the-shelf components instead of custom-made parts eliminates the need for specialized tooling and decreases lead times.
Minimizing the Number of Parts
Reducing the number of parts in a product not only simplifies its design but also streamlines assembly and reduces manufacturing time. Fewer parts mean fewer opportunities for defects, a smaller bill of materials (BOM), and lower labor costs.
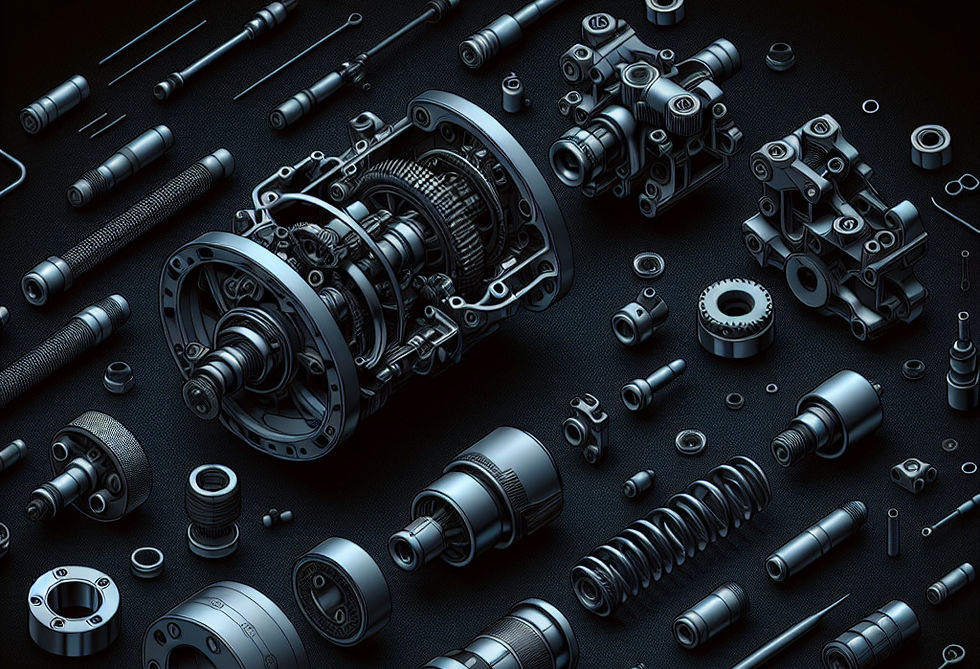
Design for Ease of Fabrication
Ease of fabrication ensures that a product’s design aligns seamlessly with the capabilities of manufacturing processes and equipment. By simplifying geometries and avoiding unnecessary complexities, manufacturers can reduce production costs and time.
Optimized Material Selection
Material selection is a critical component of DFM. Choosing the right materials can significantly impact the manufacturability, durability, and cost of a product. Designers must consider factors such as availability, compatibility with manufacturing processes, and environmental impact.

Simplified Assembly
Simplified assembly focuses on designing products that can be quickly and accurately put together, reducing production time and errors. Features like snap-fit joints, self-aligning parts, and symmetrical components make assembly easier for both human workers and automated systems.
Tolerance Optimization
Tolerance optimization ensures that dimensional variations in manufactured parts are within acceptable limits without being overly restrictive. Tight tolerances may improve precision but often increase production costs due to more stringent machining, inspection, or tooling requirements.
Error Prevention (Poka-Yoke)
Poka-Yoke, a Japanese term meaning “mistake-proofing,” refers to incorporating design features that prevent errors during manufacturing or assembly. By addressing potential errors at the design stage, manufacturers can significantly reduce defects and improve product reliability.
Benefits of DFM
Adopting DFM principles offers numerous advantages:
Cost Reduction: Streamlining designs minimizes material use, simplifies assembly, and reduces tooling needs, lowering production costs.
Improved Product Quality: Optimized designs reduce errors during production, ensuring higher-quality outcomes.
Faster Time-to-Market: Addressing manufacturability issues early avoids delays caused by redesigns or production challenges.
Sustainability: Efficient use of materials and processes aligns with environmental goals, reducing waste and energy consumption.
Enhanced Collaboration: DFM fosters teamwork between design and manufacturing teams, incorporating both perspectives for a balanced approach.
Modern Trends in DFM
Additive Manufacturing (3D Printing)
Additive manufacturing, commonly known as 3D printing, is revolutionizing product design. This layer-by-layer production method enables the creation of complex geometries and customization that were previously impossible. For DFM, additive manufacturing allows for performance-optimized designs but requires careful consideration of material properties and post-processing needs.
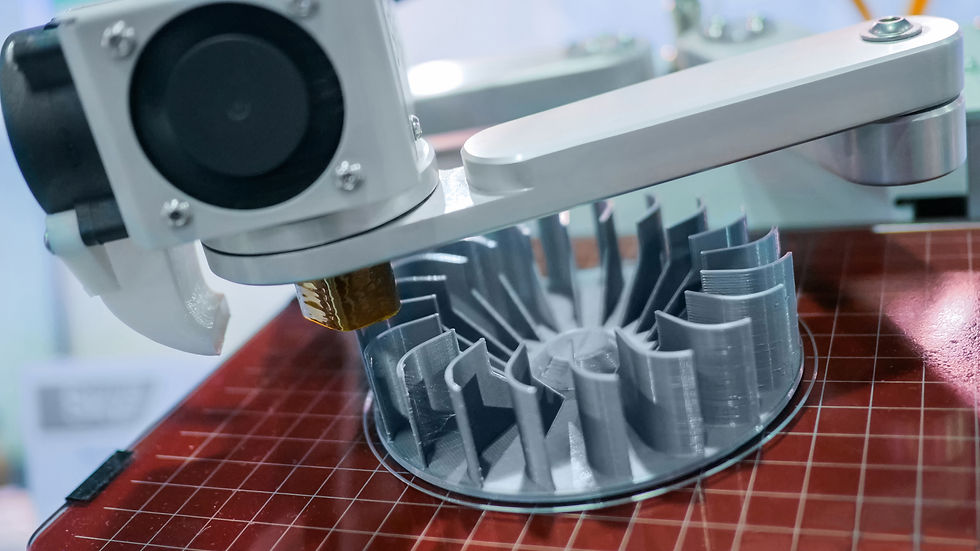
Digital Twins and Simulations
Digital twins provide virtual models of products or processes, enabling real-time analysis and optimization. By simulating manufacturing in a digital environment, designers can identify potential issues early, refine workflows, and reduce costly errors.
Artificial Intelligence
AI analyzes historical design and production data to identify optimizations and predict challenges. It enhances DFM by suggesting efficient designs, predicting defects, and automating quality control processes.
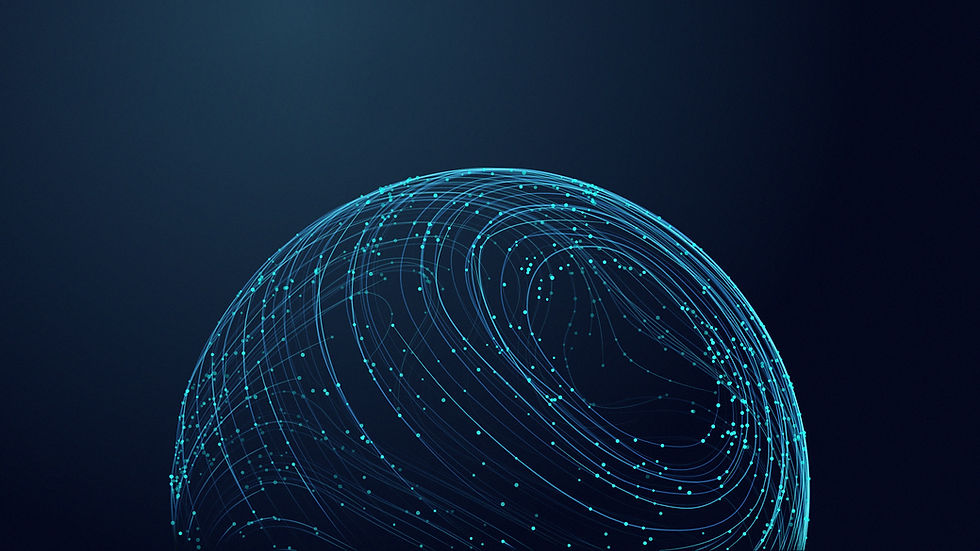
Sustainable Design Practices
Sustainable DFM prioritizes recyclability, eco-friendly materials, and energy-efficient processes. By designing for minimal waste and environmental impact, manufacturers align with regulatory standards and consumer expectations, contributing to a circular economy.
Conclusion
Design for Manufacturing (DFM) bridges the gap between innovative design and practical production, ensuring products are efficient, cost-effective, and sustainable. By integrating manufacturability early in the design phase, DFM minimizes errors, reduces costs, and speeds time-to-market. It fosters collaboration across teams and aligns products with modern demands for sustainability and efficiency.
As technologies like additive manufacturing, AI, and digital twins reshape industries, DFM evolves to support innovation while maintaining practicality. For businesses aiming to stay competitive in a dynamic market, DFM is an essential strategy for delivering high-quality, efficient, and environmentally conscious products. Contact us today to discover how Machinabilify can guide your designs from concept to market success.
Sources
"DFMA for Product Designers: A Review"Naiju, C. D. (2021).This paper discusses DFM and DFA principles for streamlining product design and manufacturing processes. Read here (PDF)
"Design for Manufacturability and Design for 'X': Concepts, Applications, and Perspectives"Kuo, T. C., & Zhang, H. C. (2001).Explores the integration of DFM with other design principles and its lifecycle applications. Read here (PDF)
"Integrated Manufacturing Features and DFM Guidelines for Reducing Product Cost"Halder, P. K., Parvez, M. S., & Szecsi, T. (2013).Discusses how integrated manufacturing features improve cost efficiency in product design. Read here (PDF)
"Towards Next-Generation Design-for-Manufacturability (DFM) Frameworks"Bajaj, M., et al. (2003).Proposes advanced frameworks for integrating DFM into electronics product realization. Read here (PDF)
"Design for Manufacture and Assembly (DfMA) in Construction: The Old and the New"Lu, W., Tan, T., & Xu, J. (2021).Discusses DFM’s adaptation in modern industries like construction, emphasizing cost efficiency and lean principles. Read here (PDF)
"An Integrated Approach for Sustainable Product Design: DFM, DFE, and CAD/CAE Principles"Chowdary, B. V., & Richards, M. A. (2019).Highlights how DFM combines with other principles for sustainable manufacturing. Read here (PDF)
"Integrated Digital Design for Manufacture for Reduced Lifecycle Cost"Curran, R., Castagne, S., & Butterfield, J. (2007).Discusses the integration of digital tools in DFM for lifecycle optimization. Read here (PDF)
"Design for Manufacturability: How to Use Concurrent Engineering for Lean Production"Anderson, D. M. (2020).This book delves into concurrent engineering approaches with a focus on DFM principles for cost-effective production. Book Access
Comments