Optimizing Product Design with DFMA: Enhancing Manufacturing and Assembly Processes
- alexandermangelo
- Oct 12, 2024
- 3 min read
Updated: Jan 5
In the competitive world of manufacturing, transforming a product idea into reality requires more than innovative design. Companies face the challenge of ensuring that their designs are practical, cost-effective, and scalable for mass production. This is where Design for Manufacturing and Assembly (DFMA) becomes an indispensable methodology. DFMA optimizes product designs by considering both the manufacturing and assembly processes, which leads to smoother production workflows, reduced costs, and improved product quality.
What Is DFMA?
Design for Manufacturing and Assembly (DFMA) is a comprehensive approach combining two key principles:
Design for Manufacturing (DFM):
This principle focuses on simplifying the manufacturing process by carefully considering material selection, ease of fabrication, and production techniques during the design phase.
Design for Assembly (DFA):
This concept emphasizes creating designs that streamline assembly, reducing the number of parts and ensuring that components fit together easily.
Together, DFM and DFA form DFMA, a strategy that helps identify inefficiencies and potential issues early in the product development cycle. This ensures that products can be efficiently manufactured and assembled with minimal complications, lower costs, and better quality outcomes.
Why Is DFMA Important?
In many companies, design teams and manufacturing departments often operate in silos, leading to mismatches between a product’s design and its manufacturability. Designers prioritize functionality and aesthetics, while manufacturers focus on practicality. Without considering manufacturing constraints during the design phase, companies can face production delays, inflated costs, and compromised product quality. DFMA bridges this gap by fostering collaboration between design and manufacturing teams early in the development process, ensuring designs are both innovative and practical for mass production.
Key Benefits of DFMA
Cost Reduction:
DFMA simplifies designs, lowering material and labor costs by reducing the number of parts in a product. Fewer components translate into less material usage, faster assembly, and decreased chances for errors.
Improved Efficiency:
Streamlined designs improve manufacturing efficiency by reducing assembly time and avoiding production bottlenecks. This enables higher output, especially important for industries with tight production schedules.
Higher Product Quality:
Simplifying designs minimizes defects and improves product reliability by reducing the number of assembly steps. Fewer components mean fewer opportunities for misalignment or improper fitting.
Sustainability and Waste Reduction:
DFMA aligns with sustainable manufacturing by optimizing material usage and reducing energy consumption. Standardizing parts across product lines allows companies to source materials more efficiently, minimizing waste and environmental impact.
Real-World Applications of DFMA
Industries like automotive, electronics, and medical devices have successfully implemented DFMA to enhance product designs and streamline production:
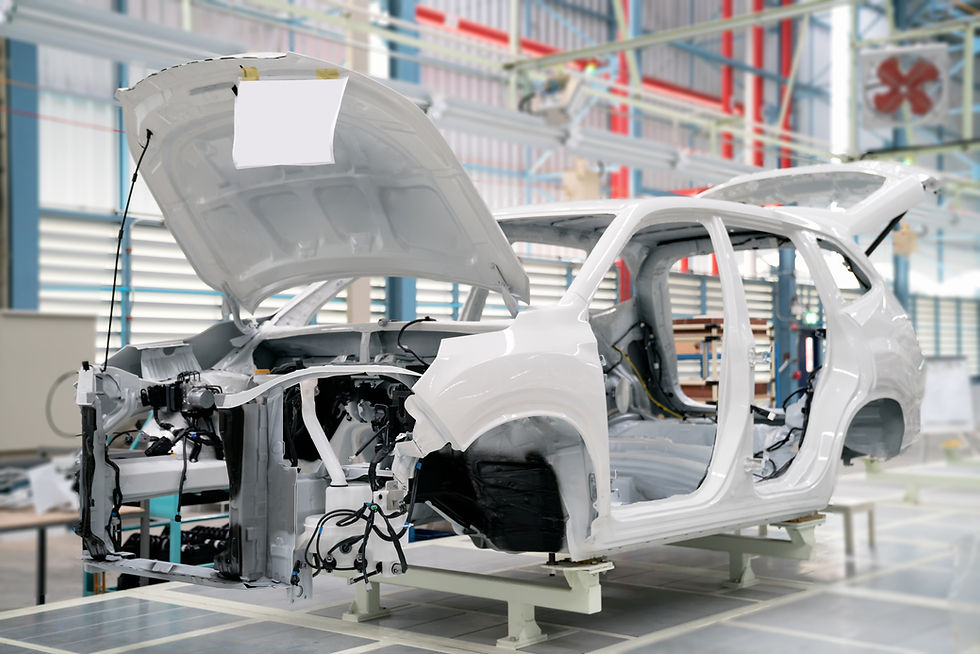
Automotive Industry:
Automakers use DFMA to reduce part counts in vehicle components, such as engine fasteners, which improves reliability and speeds up assembly.

Consumer Electronics:
In electronics, DFMA enables the production of complex devices like smartphones and laptops with fewer screws and snap-fit designs, accelerating production while maintaining quality.

Medical Devices:
DFMA helps medical device manufacturers design easy-to-assemble products with fewer failure points, ensuring consistent performance and compliance with stringent regulatory requirements.
Implementing DFMA in Your Product
Successfully adopting DFMA requires collaboration across design, engineering, and manufacturing teams. Key steps include fostering cross-functional communication, simplifying designs to reduce part counts, prototyping early to test manufacturability, and utilizing DFMA tools to analyze and improve designs. Implementing DFMA early in the process ensures a smooth transition from design to production, saving time, resources, and costs in the long run.
Conclusion
Design for Manufacturing and Assembly (DFMA) is a vital methodology for companies aiming to streamline their product development processes. By optimizing designs for manufacturing and assembly, DFMA significantly reduces costs, enhances efficiency, and improves product quality. Whether applied to new designs or existing products, DFMA ensures that products are not only innovative but also practical and cost-effective to produce.
Sources:
Boothroyd, G., Dewhurst, P., & Knight, W. (2011). Product Design for Manufacture and Assembly.
Ullman, D. G. (2010). The Mechanical Design Process.
Reinhart, G., & Schindler, S. (2011). Design for Assembly and Disassembly in Modern Manufacturing.
Chitale, A. K., & Gupta, R. C. (2013). Product Design and Manufacturing.
Pahl, G., Beitz, W., & Feldhusen, J. (2007). Engineering Design: A Systematic Approach.
Comments