Lean Six Sigma: A Powerful Approach to Process Improvement
- alexandermangelo
- Nov 3, 2024
- 7 min read
Lean Six Sigma is a hybrid methodology that combines the principles of Lean manufacturing and Six Sigma to improve business processes by eliminating waste and reducing variation. Lean focuses on streamlining operations by removing unnecessary steps and optimizing workflows, while Six Sigma emphasizes reducing defects and improving quality through statistical analysis. Together, they offer a structured approach to enhance efficiency, boost customer satisfaction, and achieve substantial cost savings. The methodology follows the DMAIC framework (Define, Measure, Analyze, Improve, Control) to systematically tackle problems, identify root causes, and implement lasting solutions. Lean Six Sigma not only addresses operational inefficiencies but also fosters a culture of continuous improvement by empowering employees to engage in problem-solving at all levels.
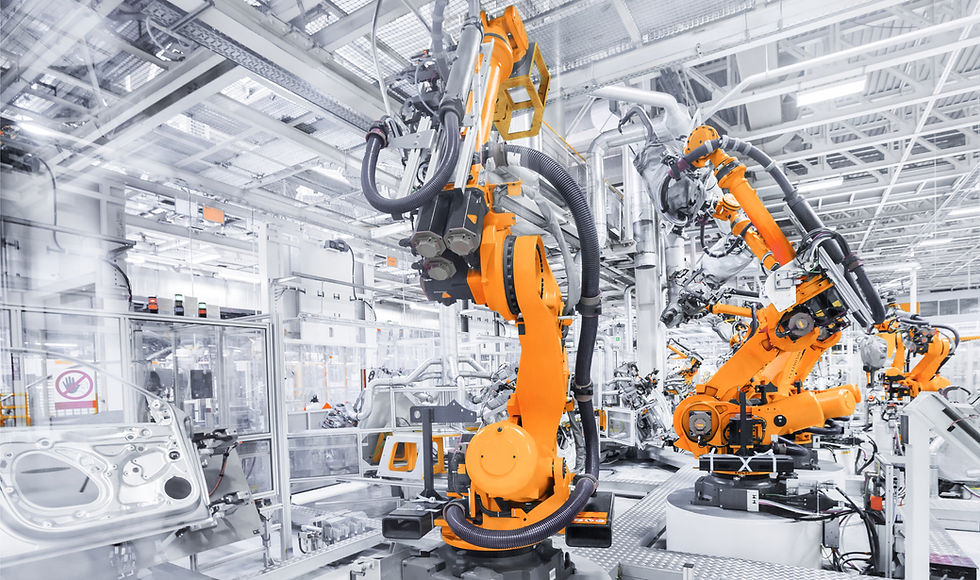
Lean Six Sigma is a hybrid methodology that combines the principles of Lean manufacturing and Six Sigma to improve business processes by eliminating waste and reducing variation. Lean focuses on streamlining operations by removing unnecessary steps and optimizing workflows, while Six Sigma emphasizes reducing defects and improving quality through statistical analysis. Together, they offer a structured approach to enhance efficiency, boost customer satisfaction, and achieve substantial cost savings. The methodology follows the DMAIC framework (Define, Measure, Analyze, Improve, Control) to systematically tackle problems, identify root causes, and implement lasting solutions. Lean Six Sigma not only addresses operational inefficiencies but also fosters a culture of continuous improvement by empowering employees to engage in problem-solving at all levels.
Key Lean Six Sigma Tools
Lean Six Sigma provides a comprehensive toolkit to diagnose, analyze, and solve process inefficiencies. Below is an expanded look at some of the most widely used tools:
DMAIC (Define, Measure, Analyze, Improve, Control):
This five-step process is foundational to Lean Six Sigma. In the Define phase, the problem and project goals are clearly outlined. Measure involves gathering data on current processes to establish a baseline. The Analyze phase uses statistical tools to identify root causes of inefficiencies or defects. In the Improve step, solutions are developed and implemented to address the root causes. Lastly, the Control phase ensures that the improvements are maintained over time, often by monitoring the process with control charts or other metrics.
Value Stream Mapping (VSM):
VSM is used to visualize the entire process flow from beginning to end, identifying every step and its contribution to value creation. By mapping out all steps involved, businesses can spot inefficiencies, bottlenecks, and waste (such as excess inventory, unnecessary waiting times, or rework). VSM aids in identifying areas where Lean principles can be applied to streamline processes.
5S:
This workplace organization method is designed to improve productivity and safety through a systematic approach: Sort (remove unnecessary items), Set in Order (organize the workspace), Shine (clean and inspect), Standardize (implement standards for organization and cleanliness), and Sustain (maintain the new order). 5S helps create a more efficient working environment by reducing clutter and improving workflow.
Kaizen:
Kaizen is a philosophy that focuses on continuous improvement through small, incremental changes. It encourages teams to constantly look for ways to improve processes, even in small ways, leading to significant long-term gains. Kaizen is not a one-time event but an ongoing process that fosters innovation and employee engagement, as everyone is encouraged to contribute to improvements.
Pareto Charts:
A Pareto Chart is a bar graph that represents the causes of problems or defects in order of importance. It is based on the 80/20 rule, where 80% of problems come from 20% of the causes. This tool helps teams prioritize issues that have the most significant impact, ensuring that resources are focused on solving the most critical problems first.
Root Cause Analysis (RCA):
RCA involves identifying the underlying causes of a problem, rather than just addressing its symptoms. The "5 Whys" technique is a common RCA tool, where the question "Why?" is asked repeatedly until the fundamental cause of the issue is found. The Fishbone Diagram (Ishikawa) is another RCA tool that helps visualize potential causes of a defect by categorizing them into groups like materials, machinery, methods, and manpower.
Statistical Process Control (SPC):
SPC uses statistical methods to monitor and control a process, ensuring that it operates at its full potential without variation. SPC tools like Control Charts help track process performance over time, flagging any deviations from expected performance. By keeping processes under control, organizations can consistently produce high-quality outputs while minimizing variation and defects.
Benefits of Lean Six Sigma

Lean Six Sigma offers a wide range of benefits, transforming operations across various industries. Here is a more detailed view of its advantages:
Increased Efficiency:
By eliminating non-value-added activities, Lean Six Sigma helps businesses improve the efficiency of their operations. Streamlining processes results in faster cycle times and quicker turnaround, which reduces operational delays. For example, unnecessary movements in production, excess waiting times, and over processing are all eliminated through Lean tools, making the workflow more straightforward and time-efficient. This allows companies to serve customers faster, increase production throughput, and reduce operating costs without sacrificing quality.
Enhanced Quality:
Six Sigma’s data-driven focus on reducing defects ensures that product and service quality is consistently improved. By using tools like Statistical Process Control (SPC) and Root Cause Analysis (RCA), organizations can identify and address the variations that lead to defects. This focus on quality control leads to fewer errors in production, fewer customer complaints, and fewer product recalls or rework. Over time, the improved quality can elevate a company’s reputation in the marketplace, increasing brand loyalty and repeat business.
Cost Savings:
Lean Six Sigma’s combined focus on waste reduction and defect elimination translates directly into cost savings. Companies can significantly reduce waste in materials, labor, and time by streamlining processes and improving quality control. Reduced defects mean less rework, fewer resources wasted on faulty products, and more efficient use of labor. Additionally, optimized processes often require less energy and materials, contributing to operational savings. These cumulative cost reductions can have a substantial impact on the company's bottom line, increasing profitability.
Data-Driven Decision Making:
One of the core principles of Six Sigma is using statistical data to drive process improvements. This results in better decision-making, as actions are based on reliable data rather than assumptions. Data analysis allows businesses to identify process bottlenecks, variability, and inefficiencies with precision. As a result, managers can make informed decisions backed by empirical evidence, reducing the risks associated with implementing process changes and ensuring that improvements are sustainable over time.
Employee Engagement:
Lean Six Sigma empowers employees at all levels to contribute to process improvement initiatives. By involving workers in the identification of problems and the development of solutions, it fosters a culture of engagement and innovation. Employees on the front lines often have the best understanding of where inefficiencies lie, and Lean Six Sigma encourages them to contribute their insights. This level of participation improves morale, creates a sense of ownership, and promotes teamwork, which in turn leads to a more dynamic and productive workplace.
Customer Satisfaction:
Lean Six Sigma’s combined focus on speed, quality, and defect reduction directly translates into higher customer satisfaction. Faster delivery times, fewer product defects, and consistent quality ensure that customers receive products or services that meet or exceed their expectations. This enhanced customer experience can lead to increased loyalty, repeat business, and positive word-of-mouth referrals, all of which contribute to the company’s growth and success. In today’s competitive marketplace, consistently delivering high-quality products on time is a key factor in differentiating a brand.
Adaptability:
One of the greatest strengths of Lean Six Sigma is its adaptability. It can be applied across industries, from manufacturing to healthcare, finance, and even service industries. The principles of reducing waste and improving quality are universally applicable, allowing companies in any sector to improve their operations. Whether dealing with production line inefficiencies, administrative bottlenecks, or customer service challenges, Lean Six Sigma offers tools and methodologies that can be customized to fit specific business needs. This flexibility makes it a powerful tool for continuous improvement in a wide variety of settings.
How Do Lean and Six Sigma Work Together to Improve Business Processes?
Lean and Six Sigma complement each other by addressing different aspects of process improvement. Lean focuses on eliminating waste, such as excessive waiting times, overproduction, and unnecessary motions, thereby streamlining operations. Six Sigma, on the other hand, targets process variation and defects through rigorous data analysis and quality control. When combined, Lean accelerates process flow while Six Sigma ensures that the processes remain consistent and defect-free. By integrating these approaches, businesses can not only improve speed and efficiency but also enhance quality, creating a balanced approach to process optimization. This combination enables organizations to reduce cycle times, improve operational reliability, and consistently meet customer expectations.
What Are the Most Effective Lean Six Sigma Tools for Reducing Waste?
Several Lean Six Sigma tools are particularly effective for reducing waste and enhancing efficiency. Value Stream Mapping (VSM) is one of the most important tools, helping organizations visualize and analyze the entire production flow to identify waste and bottlenecks. 5S is another crucial tool that improves workplace organization by eliminating unnecessary items and standardizing processes. This leads to reduced motion waste and improved operational efficiency. Kaizen encourages continuous, small-scale improvements that lead to substantial long-term reductions in waste. Additionally, Root Cause Analysis tools, such as the 5 Whys and Fishbone Diagram, help teams pinpoint the underlying causes of wasteful practices, enabling more targeted solutions. These tools, when applied together, allow businesses to systematically identify and eliminate non-value-added activities.
How Does Lean Six Sigma Improve Customer Satisfaction?

Lean Six Sigma improves customer satisfaction by ensuring that products and services consistently meet or exceed customer expectations in terms of quality, delivery, and reliability. By reducing process inefficiencies and defects, Lean Six Sigma ensures that customers receive high-quality products with fewer errors, leading to greater satisfaction. The speed improvements driven by Lean principles also result in faster delivery times, which customers highly value. Additionally, by engaging employees at all levels in continuous improvement efforts, Lean Six Sigma fosters a customer-centric culture, where every process is optimized to provide better value to the customer. This holistic approach to process improvement results in products and services that are more reliable, delivered faster, and tailored to the needs and expectations of the customer, thereby driving higher loyalty and repeat business.
Conclusion
Lean Six Sigma remains a cornerstone for companies seeking to drive operational excellence, enhance customer satisfaction, and foster continuous improvement in dynamic environments. By applying a combination of Lean’s waste reduction and Six Sigma’s precision in eliminating defects, organizations can achieve sustainable growth and competitive advantage.
Sources and References:
George, M. L. Lean Six Sigma: Combining Six Sigma with Lean Speed. McGraw-Hill, 2002.
Womack, J. P., & Jones, D. T. Lean Thinking: Banish Waste and Create Wealth in Your Corporation. Free Press, 2003.
Pande, P. S., Neuman, R. P., & Cavanagh, R. R. The Six Sigma Way: How GE, Motorola, and Other Top Companies are Honing Their Performance. McGraw-Hill, 2000.
Liker, J. K. The Toyota Way: 14 Management Principles from the World's Greatest Manufacturer. McGraw-Hill, 2004.
Antony, J., & Banuelas, R. Key Ingredients for the Effective Implementation of Six Sigma Program. Measuring Business Excellence, 2002.
Snee, R. D. Lean Six Sigma – Getting Better All the Time. International Journal of Lean Six Sigma, 2010.
Comments