How to Cut Manufacturing Costs with Better Design
- alexandermangelo
- Feb 12
- 3 min read
Manufacturing costs are a significant factor in the profitability and success of any product. Many companies focus on sourcing cheaper materials or outsourcing labor to reduce expenses, but one of the most effective ways to lower costs is through better product design. By integrating Design for Manufacturing (DFM) principles, businesses can streamline production, minimize waste, and enhance efficiency, all while maintaining product quality.
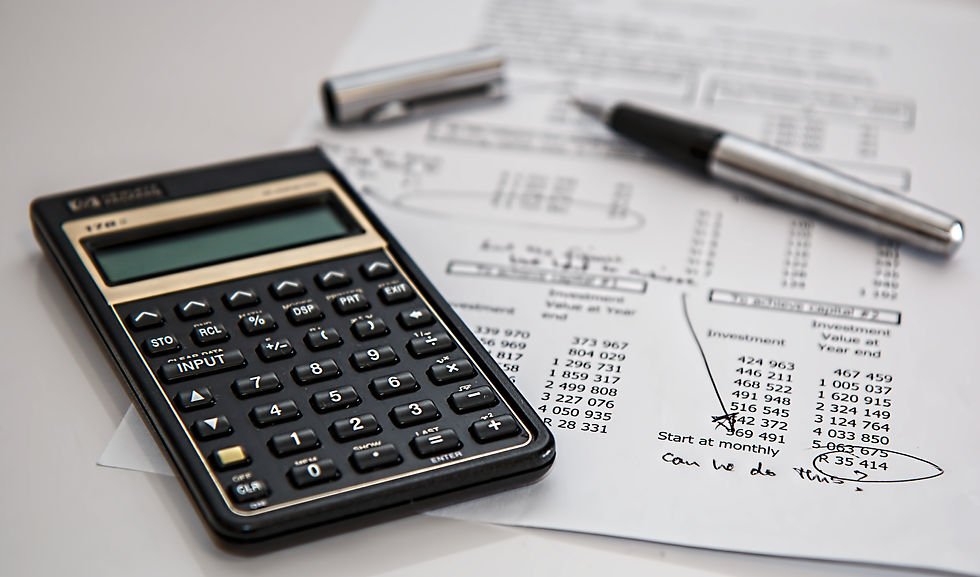
In this blog, we’ll explore how optimal design choices can significantly cut manufacturing costs and improve overall product development.
1. Embrace Design for Manufacturing (DFM)

Design for Manufacturing (DFM) is a strategic approach that ensures a product is designed in a way that simplifies production and assembly. This method reduces the number of processes needed, minimizes errors, and enhances overall efficiency. Key principles of DFM include:
Reducing Part Count: Simplifying the product structure lowers material costs, assembly time, and the chances of defects.
Standardizing Components: Using common, off-the-shelf parts instead of custom ones can significantly reduce costs and lead times.
Minimizing Complex Geometries: Avoiding unnecessary design complexities ensures easier machining, molding, and assembly.
By incorporating these principles early in the product development phase, businesses can avoid expensive modifications later.
2. Optimize Material Selection

The choice of materials plays a crucial role in manufacturing cost. While high-quality materials may seem like the best option, they are not always necessary. A cost-effective approach to material selection includes:
Using Alternative Materials: Advances in material science offer cheaper yet durable substitutes to expensive metals and composites.
Reducing Material Waste: Design components to maximize material usage and minimize scrap during fabrication.
Weight Reduction: Lighter products require less raw material and reduce shipping costs, particularly in industries like automotive and aerospace.
Proper product design ensures that the chosen materials align with both functionality and cost-effectiveness.
3. Improve Manufacturing Processes

A well-designed product should align with the most efficient manufacturing processes available. Companies can save money by selecting processes that:
Require Fewer Manufacturing Steps: Reducing the number of steps in production, such as eliminating unnecessary machining or surface finishing, decreases costs.
Utilize Automation-Friendly Designs: Ensuring that products can be easily assembled using automation improves efficiency and consistency.
Support Scalable Production: Designing with mass production in mind allows for bulk manufacturing, reducing per-unit costs.
For example, injection molding is often more cost-effective for plastic components than CNC machining, provided the design is optimized for molding.
4. Simplify Assembly and Reduce Labor Costs
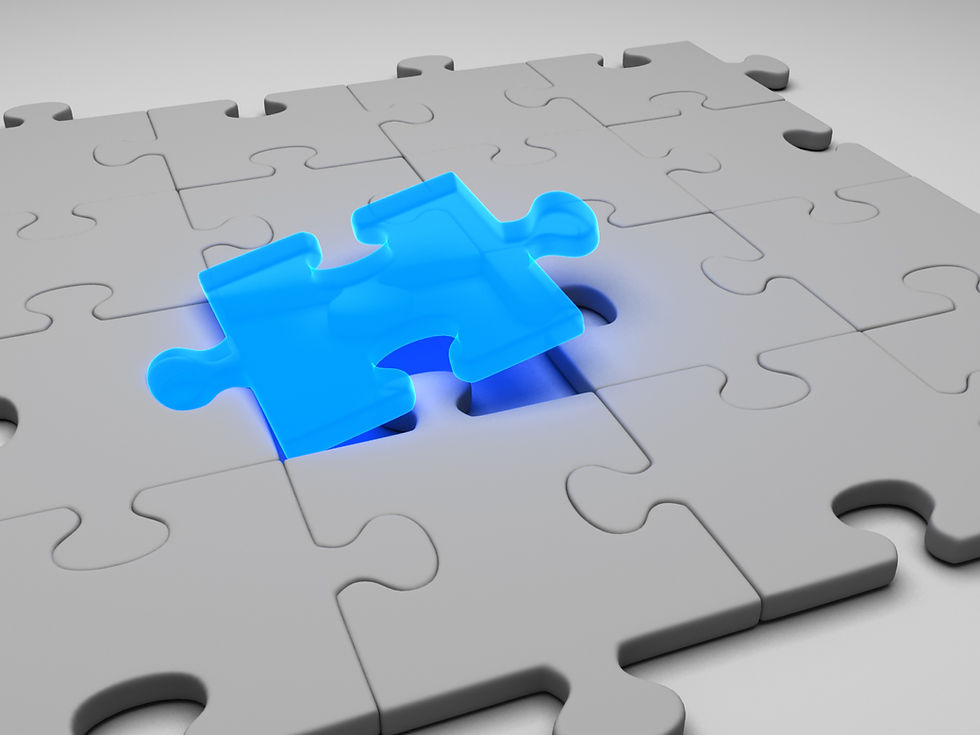
A complex assembly process increases labor costs and introduces the potential for errors. Optimizing the design for assembly leads to:
Faster Production Cycles: Fewer components and simpler assembly mean products can be built quickly.
Lower Labor Costs: Reducing manual intervention lowers manufacturing expenses.
Improved Quality Control: Standardized assembly reduces human errors and enhances product consistency.
For example, designing snap-fit connections instead of screws or adhesives can reduce assembly time and costs.
5. Conduct Cost-Driven Prototyping

Prototyping is essential in product development, but without a strategic approach, it can become an expensive process. Cost-effective prototyping strategies include:
Using 3D Printing for Initial Designs: Additive manufacturing is a low-cost way to test concepts before investing in full-scale production.
Building Functional Prototypes Early: Identifying and fixing design flaws in the prototype phase prevents costly revisions later.
Testing for Manufacturability: Ensuring that a design can be efficiently manufactured reduces unexpected production costs.
Integrating manufacturability testing during prototyping prevents costly redesigns and delays.
6. Collaborate with Manufacturers Early

Many design flaws that increase manufacturing costs stem from a lack of collaboration between engineers and manufacturers. Early communication with production teams ensures:
Feasible Designs: Manufacturers can suggest cost-effective design modifications.
Efficient Tooling and Fixtures: Proper planning reduces setup costs and production downtime.
Improved Supply Chain Management: Designers can work with suppliers to choose cost-effective materials and components.
By involving manufacturers early in the product design process, companies can avoid costly mistakes and streamline production.
7. Leverage Simulation and Digital Tools

Modern product design benefits from advanced simulation software that helps engineers refine designs before production begins. Digital tools allow companies to:
Identify Weak Points: Structural simulations help reduce material usage without compromising strength.
Optimize Manufacturing Processes: Virtual simulations test different production methods to find the most efficient one.
Reduce Prototyping Costs: Digital testing eliminates the need for multiple physical prototypes.
By using tools like finite element analysis (FEA) and computational fluid dynamics (CFD), businesses can achieve an optimal design while lowering costs.
Conclusion
Cutting manufacturing costs through better product design is a smart, sustainable approach to improving profitability. By integrating Design for Manufacturing (DFM) principles, optimizing materials and processes, simplifying assembly, and leveraging modern digital tools, companies can significantly reduce production expenses without sacrificing quality.
For businesses looking to stay competitive, investing in optimal design is not just an option—it’s a necessity. By designing smarter, companies can enhance efficiency, reduce costs, and improve market success.
Would you like expert guidance on optimizing your product development process? Contact us today to learn how better design can transform your manufacturing efficiency!
コメント